Types and Features of Nonwoven Fabric Manufacturing Processes
The characteristics of nonwoven fabrics are significantly influenced by factors such as the arrangement, bonding state, and strength of the fibers. These elements are determined by the choices and operations involved in the manufacturing process.
This page explains the common manufacturing processes for nonwoven fabrics from two perspectives: “the sequence of manufacturing processes” and “key methods in each process and their effects on nonwoven fabrics.”
Related Page: What is Nonwoven Fabric?
Table of Contents
Overview of Nonwoven Fabric Manufacturing Processes
First, let’s look at the key steps involved in manufacturing nonwoven fabrics.
The manufacturing process can be broadly divided into four stages: raw material selection, web (*1) formation, web bonding, and finishing treatments.
Below is a summary of each process and its impact on nonwoven fabrics.
(*1) In nonwoven fabric manufacturing, a web refers to a layer or sheet of fibers that are either randomly oriented or aligned in one direction.
Raw Material Selection
The first step in raw material selection is determining the type of fiber. Major fiber types include natural fibers, chemical fibers, synthetic fibers, and regenerated fibers. Each fiber type offers unique functional characteristics; for example, natural fibers excel in absorbency and flexibility, whereas synthetic fibers are known for durability and strength.
The shape of the fibers is also a critical factor. Fiber length, diameter, and cross-sectional shape directly influence the strength, flexibility, and texture of the nonwoven fabric.
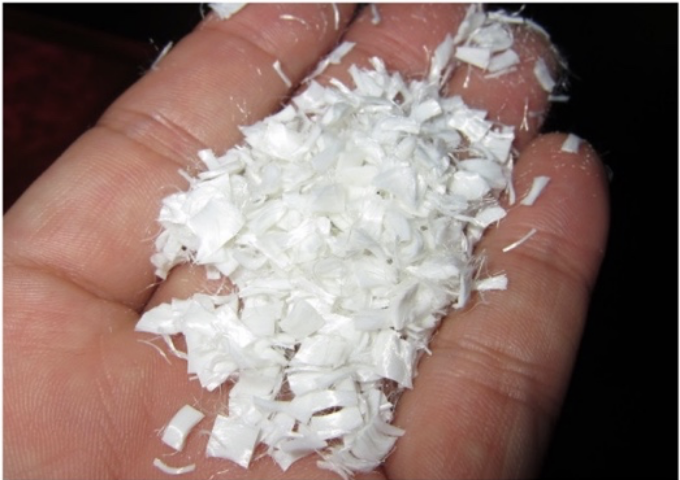
Web Formation
Using the selected raw materials, a web is formed. In this stage, the alignment of fibers is critical, as it determines whether the nonwoven fabric’s strength will be uniform or reinforced in a specific direction.
Density and thickness are also controlled during this stage. These factors directly affect the fabric’s breathability, permeability, and insulation properties.

Web Bonding
The formed web is bonded using physical or chemical methods. The bonding method selected greatly impacts the fabric’s strength, elasticity, and durability.
Uniform bonding is essential because uneven bonding can lead to variations in strength, resulting in reduced quality.
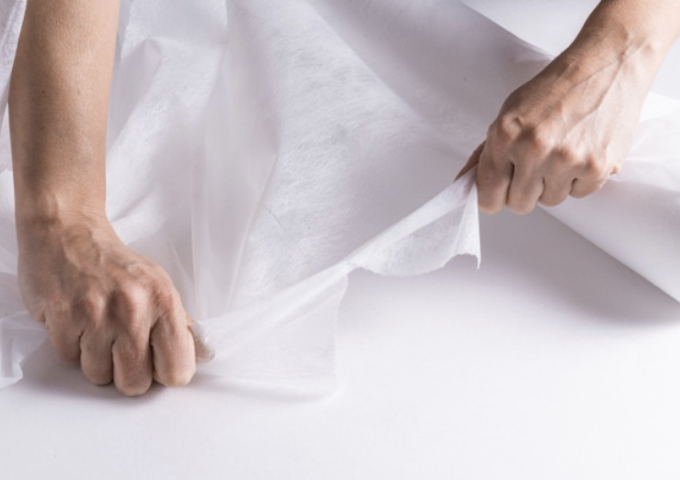
Finishing Treatments
Special chemical or surface treatments are applied to the bonded web to add functionality such as water repellency, flame resistance, or antibacterial properties. Surface processing not only enhances performance but also affects the texture and appearance of the fabric. These treatments enable nonwoven fabrics to be used in a wide range of applications, from everyday items to industrial and medical products.
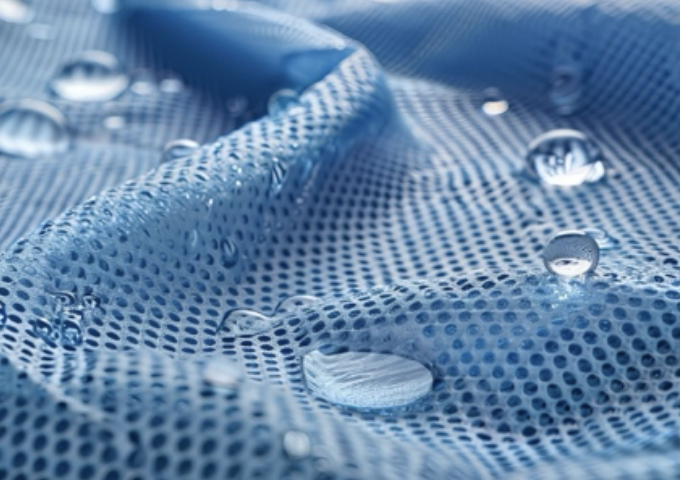
As described above, the manufacturing process is closely tied to the overall quality and performance of nonwoven fabrics, from the micro-level arrangement of fibers to the final product’s functional characteristics.
Types and Features of Web Formation Methods in Nonwoven Fabric Manufacturing
Next, we delve into the methods used in the web formation process.
As mentioned earlier, web formation involves arranging fibers into a specific sheet-like structure.
The following are the main methods used in this process:
Drylaid
Fibers are arranged mechanically in a dry state to form a web. Drylaid methods can be further divided into airlaid and carded methods.
Airlaid
Fibers are transported by air and randomly arranged to form a web. This method is suitable for products requiring high absorbency.
Carded
Fibers are aligned using a carding machine, resulting in a relatively uniform and oriented web.
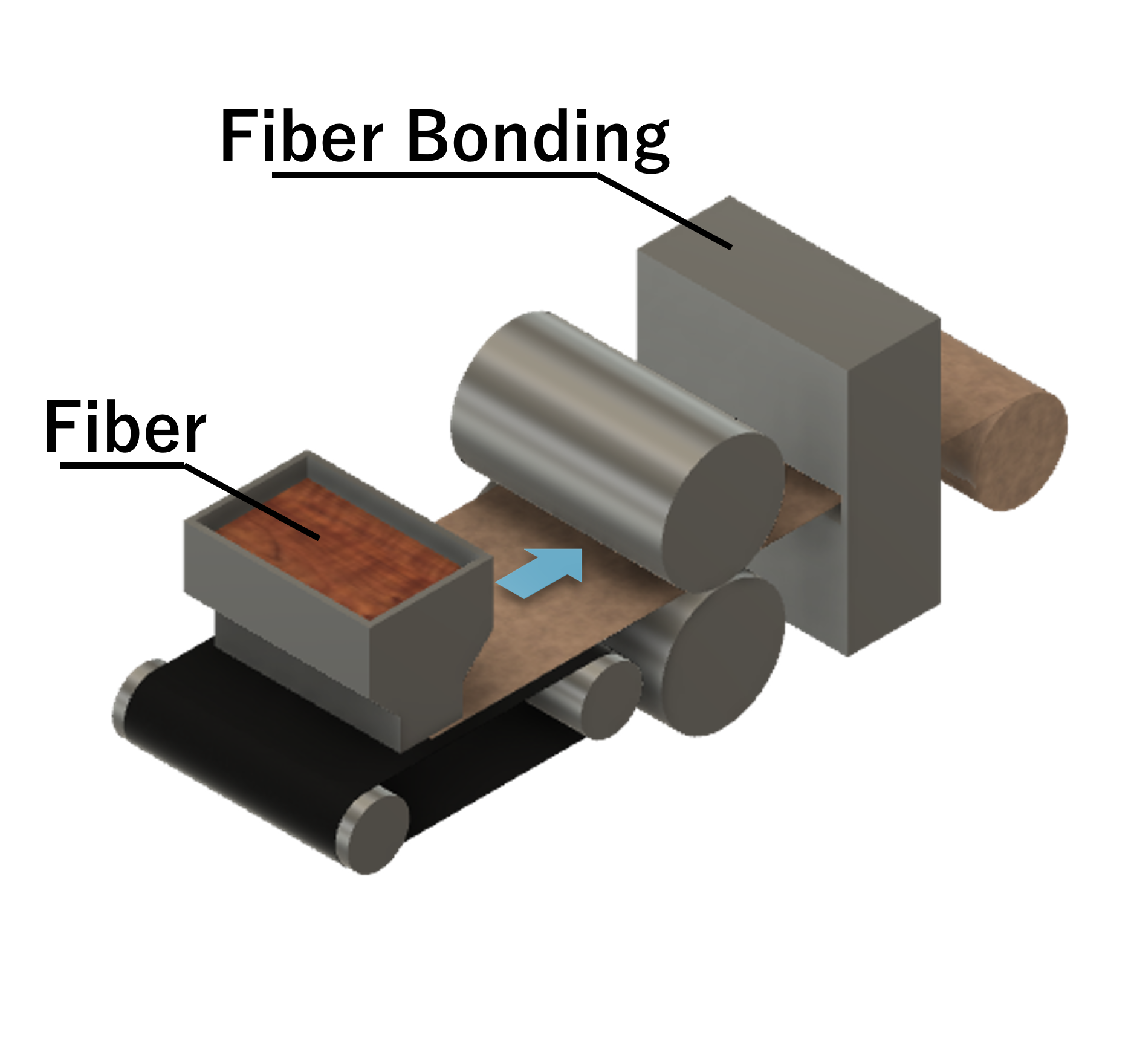
Wetlaid
Fibers are dispersed in water or another liquid and then filtered onto a screen to form a web. This method, similar to paper production, creates uniform, high-density webs. Our company specializes in this wetlaid method, producing “wet-laid nonwoven fabrics” known for their uniformity and soft texture, widely used in industrial materials, food packaging, and medical products.
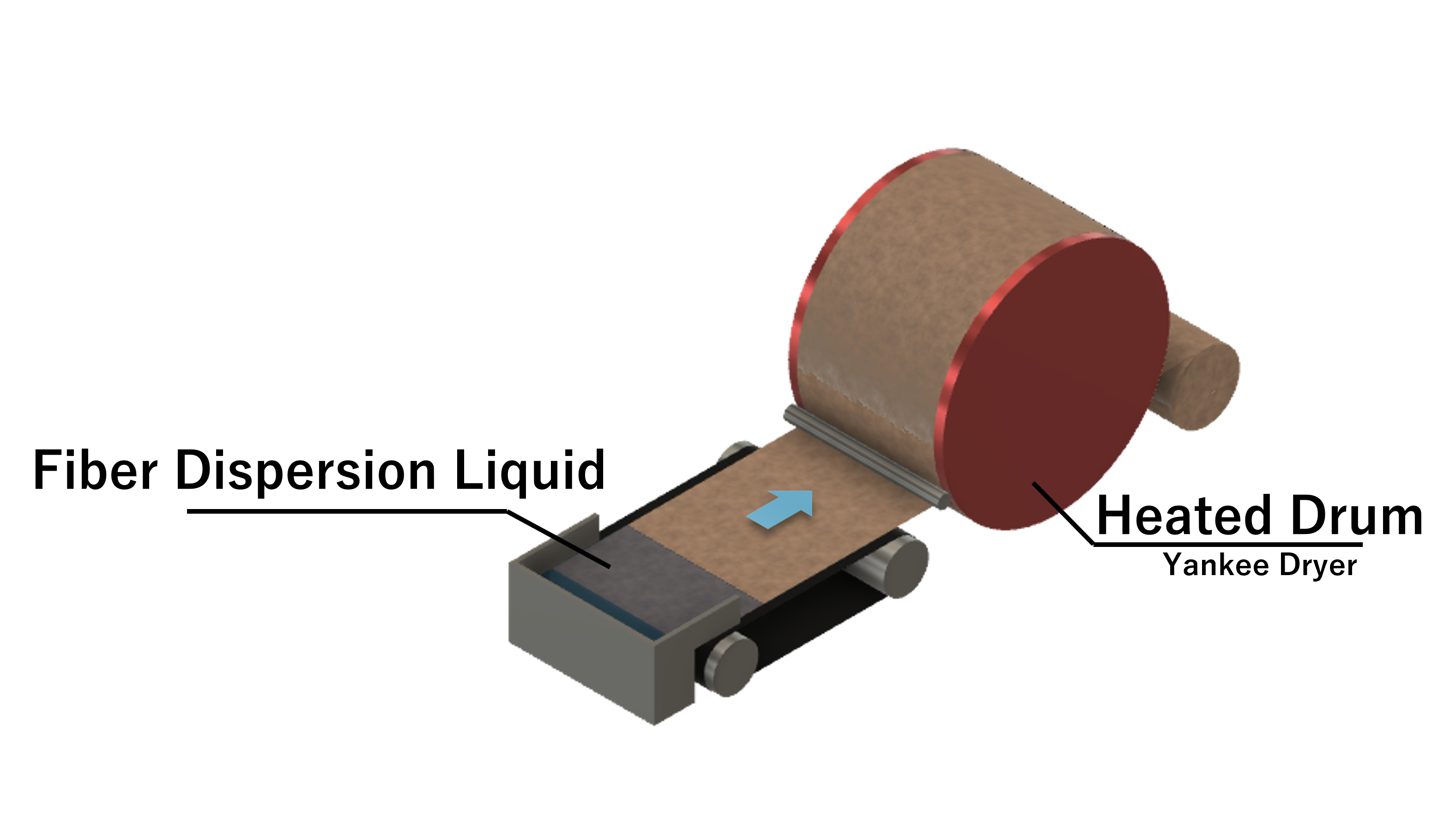
Meltblown
Polymers are melted and extruded through nozzles with fine holes. High-speed hot air stretches the molten polymers into extremely fine fibers, which are then randomly arranged. This method is ideal for applications requiring high filtration efficiency.
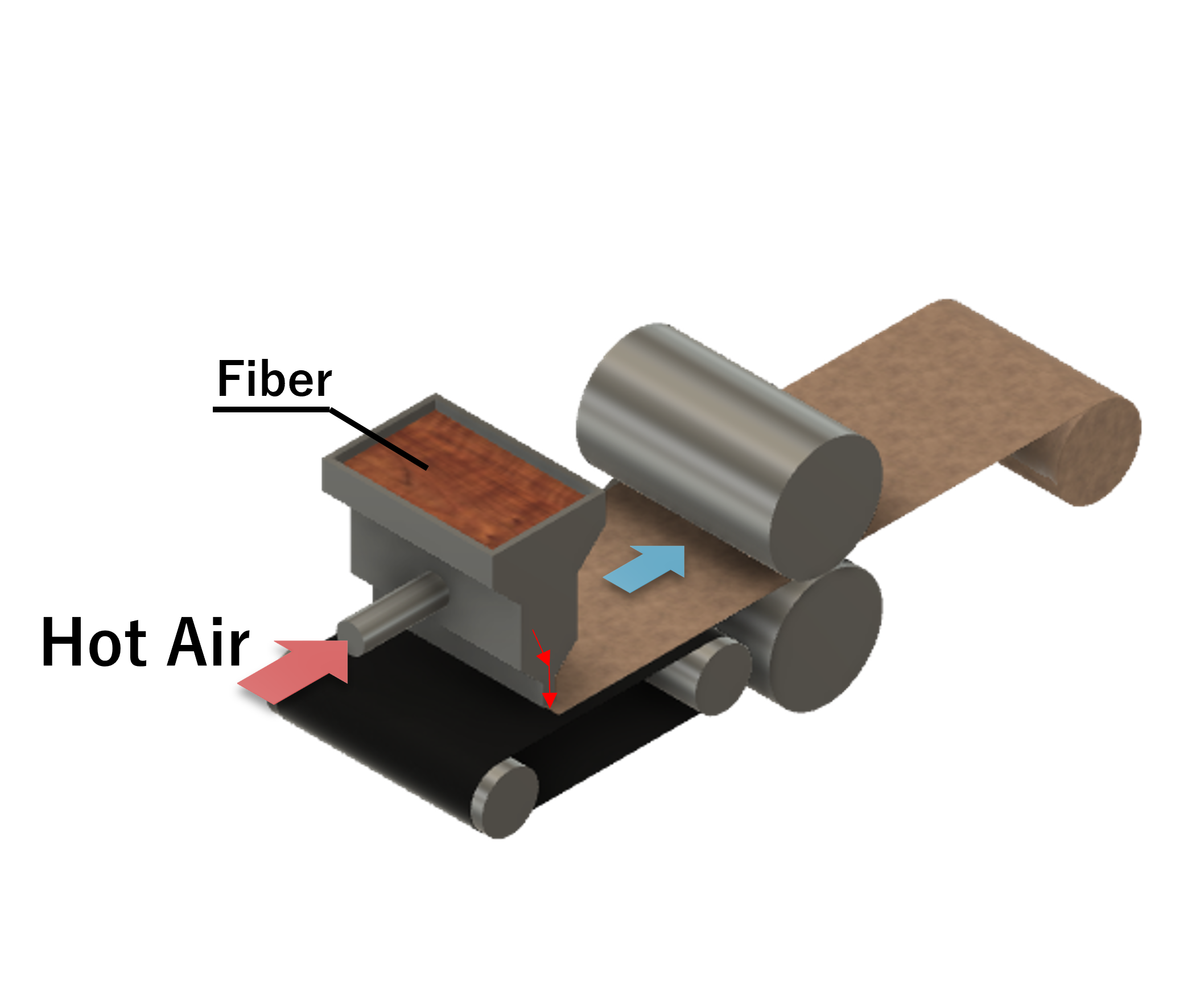
Spunbond
Polymers are melted, extruded into fine filaments, cooled, and arranged into a web. Unlike meltblown, spunbond fibers are thicker and longer, resulting in high-strength and durable fabrics.
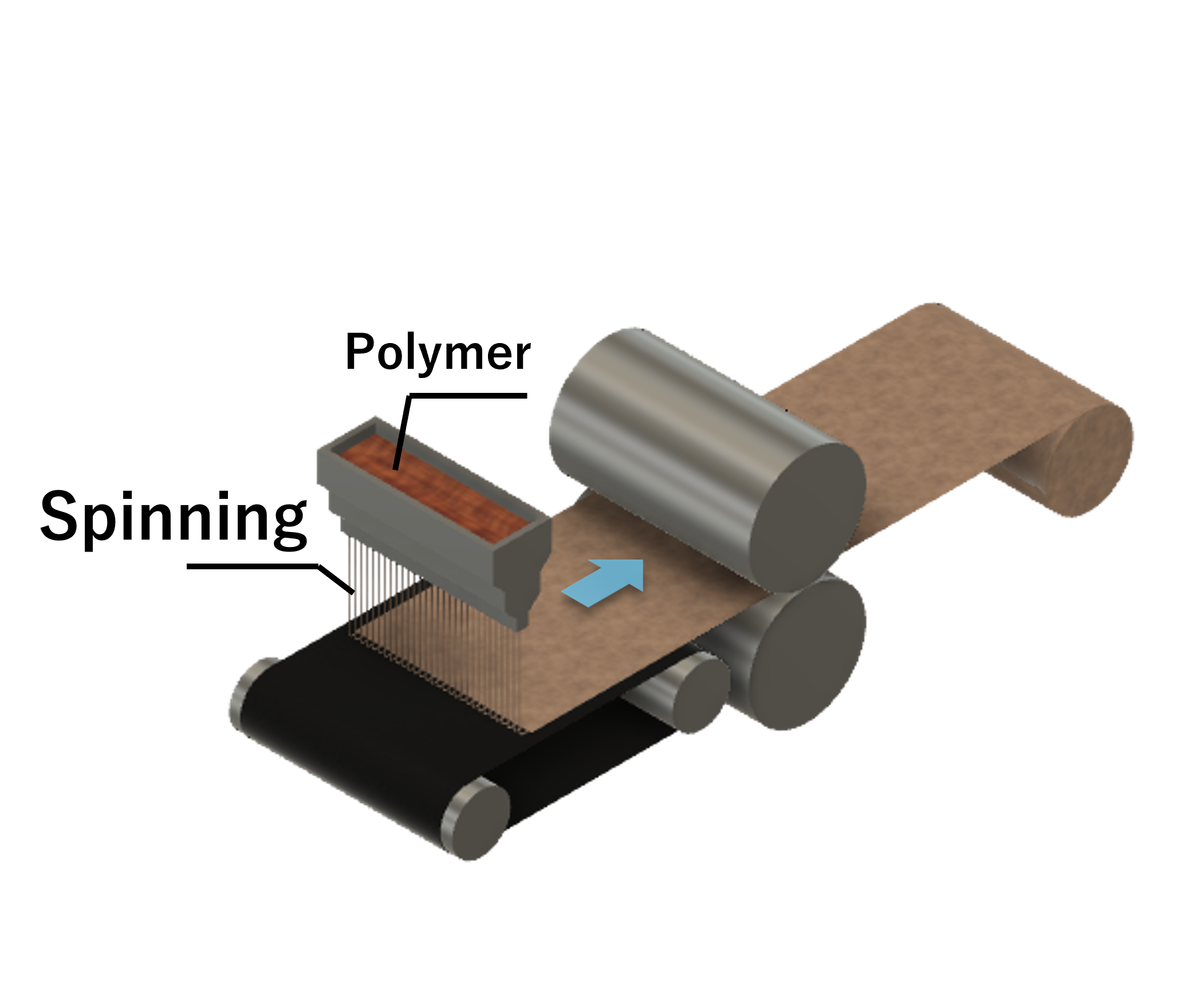
Flash Spun
Polymers dissolved in solvents are rapidly evaporated under high pressure to create fibers, which are assembled into a web. The resulting web is lightweight and offers excellent barrier properties.
As with web formation, selecting the appropriate bonding method significantly influences the physical properties and intended use of nonwoven fabrics.
Types and Features of Web Bonding Methods
After web formation, fibers are bonded to create a fabric with strength and specific physical properties. Bonding methods are broadly categorized into mechanical bonding, chemical bonding, solvent bonding, and thermal bonding. Below are the details of each method:
Mechanical Bonding
Needle Punching
Special needles repeatedly pierce the web, physically entangling the fibers. This method is suitable for producing thick and durable fabrics.
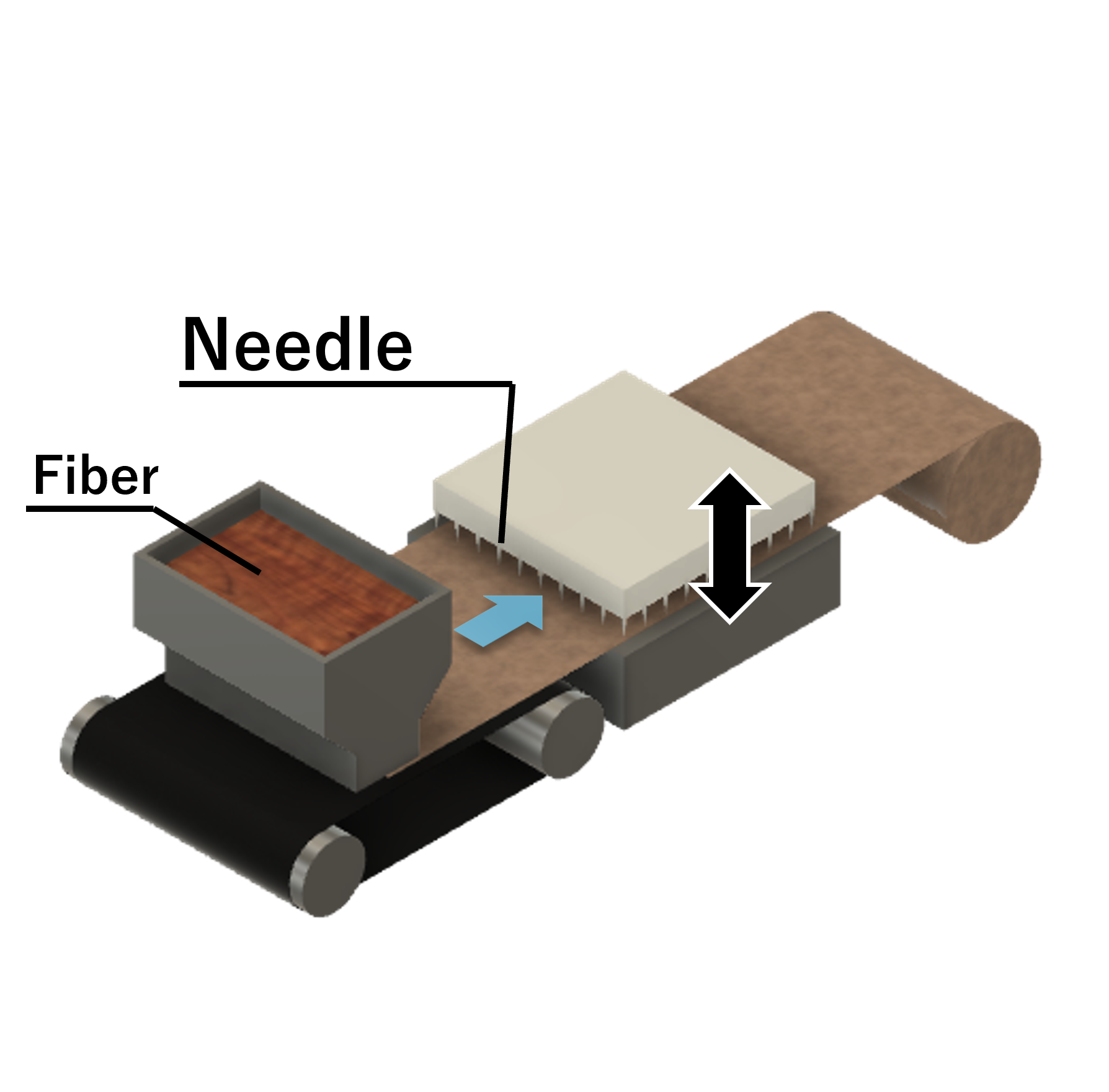
Hydroentangling
High-pressure water jets entangle fibers. Known as “spunlace,” this process creates soft and skin-friendly fabrics.
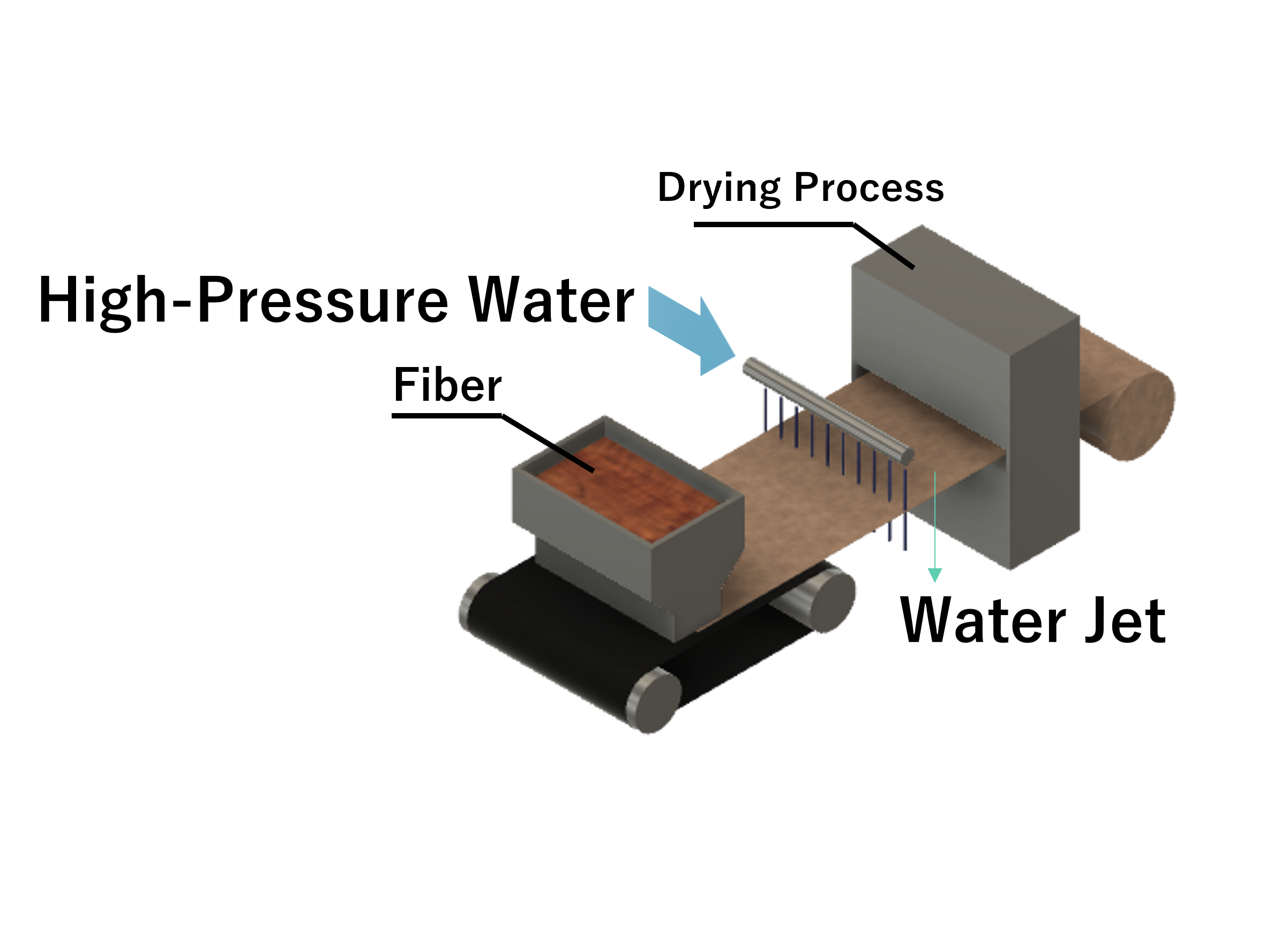
Thermal Bonding
Heat and pressure are applied to fuse thermoplastic fibers in the web, producing uniform and strong fabrics.
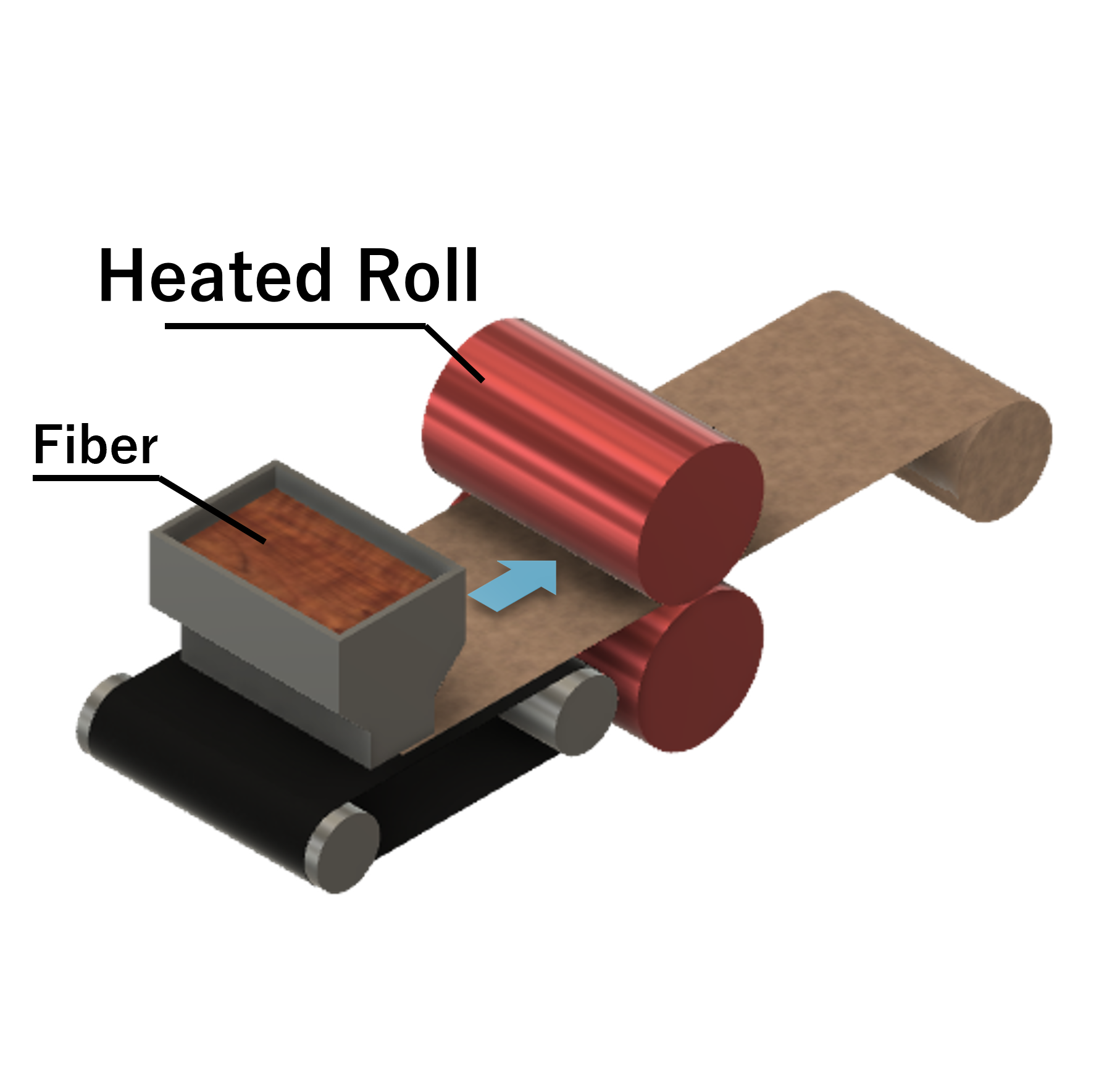
Chemical Bonding
Adhesive Bonding
Water- or solvent-based adhesives are used to bond fibers, suitable for applications requiring specific functionalities.
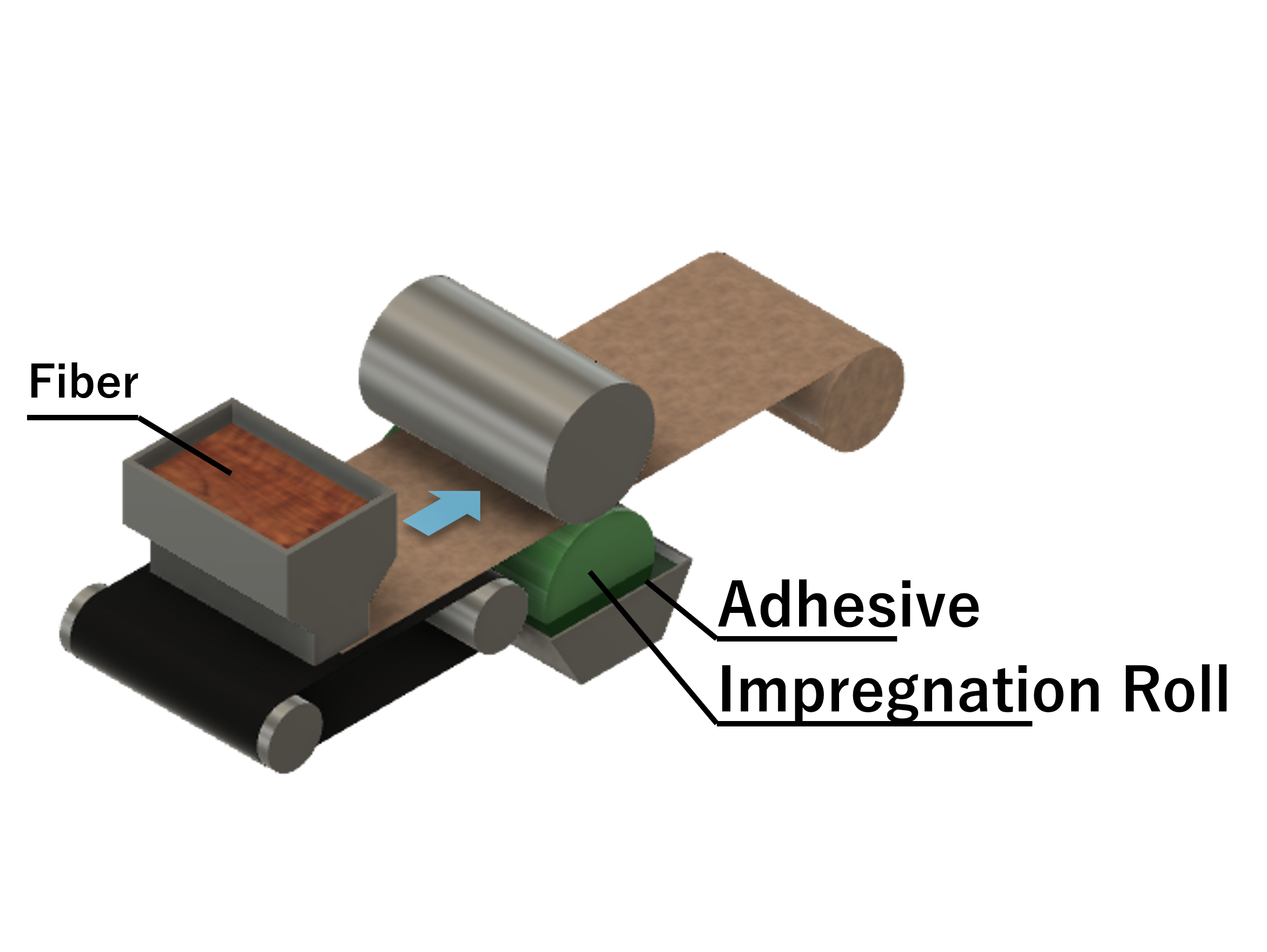
Print Bonding
Adhesives are printed in specific patterns on the web, and heat is applied to bond the fibers. This method produces fabrics with unique textures or patterns.
Solvent Bonding
Solvent Bonding
Solvents partially dissolve specific fibers in the web, which bond as they dry. This method is ideal for creating fabrics with exceptionally smooth surfaces.
Thermal Bonding
Calendering
The web is passed through heated rollers to apply pressure, to bond the fibers and smooth the surface.
As with web formation, selecting the appropriate bonding method significantly influences the physical properties and intended use of nonwoven fabrics.
Types and Features of Finishing Treatments
The final step involves finishing treatments to add specific properties or functionalities to the nonwoven fabric, improving its performance, appearance, or texture. Common finishing treatments include:
Water- and Oil-Repellent Treatments
Prevent liquid penetration and are suitable for hygiene products, medical supplies, and construction materials.
Antibacterial and Deodorizing Treatments
Use chemicals or natural agents to inhibit bacterial growth and odors, ideal for hygiene products, filters, and clothing.
Softening and Hardening Treatments
Enhance texture using softeners or harden specific areas with resins for shape retention.
Flame-Resistant Treatments
Add flame-retardant properties for applications such as construction materials, automotive interiors, and clothing.
Dyeing and Printing Treatments
Add colors or patterns, suitable for clothing, decorative items, and promotional materials.
UV Protection Treatments
Prevent UV damage, enhancing durability for outdoor products and clothing.
Surface Processing (e.g., Embossing)
Add textures or patterns for improved aesthetics, grip, or functionality.
These finishing treatments can transform nonwoven fabrics into products suitable for a wide range of applications, addressing specific requirements and enhancing overall performance.
Feel Free to Consult Us About Nonwoven Fabrics
The features and functionalities of nonwoven fabrics vary greatly depending on the manufacturing methods and materials used. Achieving the desired characteristics for specific purposes can be a challenging task.
Hirose Paper Mfg Co., Ltd. has been dedicated to nonwoven fabric research and development since its establishment in 1958. Building on our success as the first in Japan to develop wet-laid nonwoven fabrics using synthetic fiber vinylon, we have pursued world-class technologies for over 60 years. Our innovations include 100% synthetic fiber nonwoven fabrics, the world’s thinnest papermaking technology (2g/m² with 100% polyolefin fibers), and electrospun nanofibers for various applications such as lithium-ion battery separators, functional air filters, and medical products.
For any questions about nonwoven fabrics, our expert team is ready to assist you.