High-Performance Materials as Alternatives to PFAS
In recent years, PFAS (Per- and Polyfluoroalkyl Substances) regulations have been rapidly advancing worldwide, driving increased demand for alternative materials in various industries. This article delves into candidate materials for replacing PFAS while exploring the reasons behind PFAS regulations.
Table of Contents
What Are PFAS Regulations?
PFAS regulations refer to legal measures and standards aimed at restricting or managing the manufacture, use, and release of substances defined as PFAS. PFAS are synthetic organic fluorinated compounds characterized by their strong carbon-fluorine (C-F) bonds. These bonds impart exceptional properties such as heat resistance, chemical resistance, and water- and oil-repellency, making PFAS highly valuable for applications in coatings, resins, and more.
However, PFAS are persistent in the environment and pose potential risks to human health and ecosystems. Certain compounds like PFOS (Perfluorooctane Sulfonate) and PFOA (Perfluorooctanoic Acid) have already been restricted or banned in many countries, including Japan, due to their harmful effects. With ongoing discussions about extending regulations to other PFAS, industries face the urgent task of developing viable alternatives.
Candidate Materials for Replacing PFAS
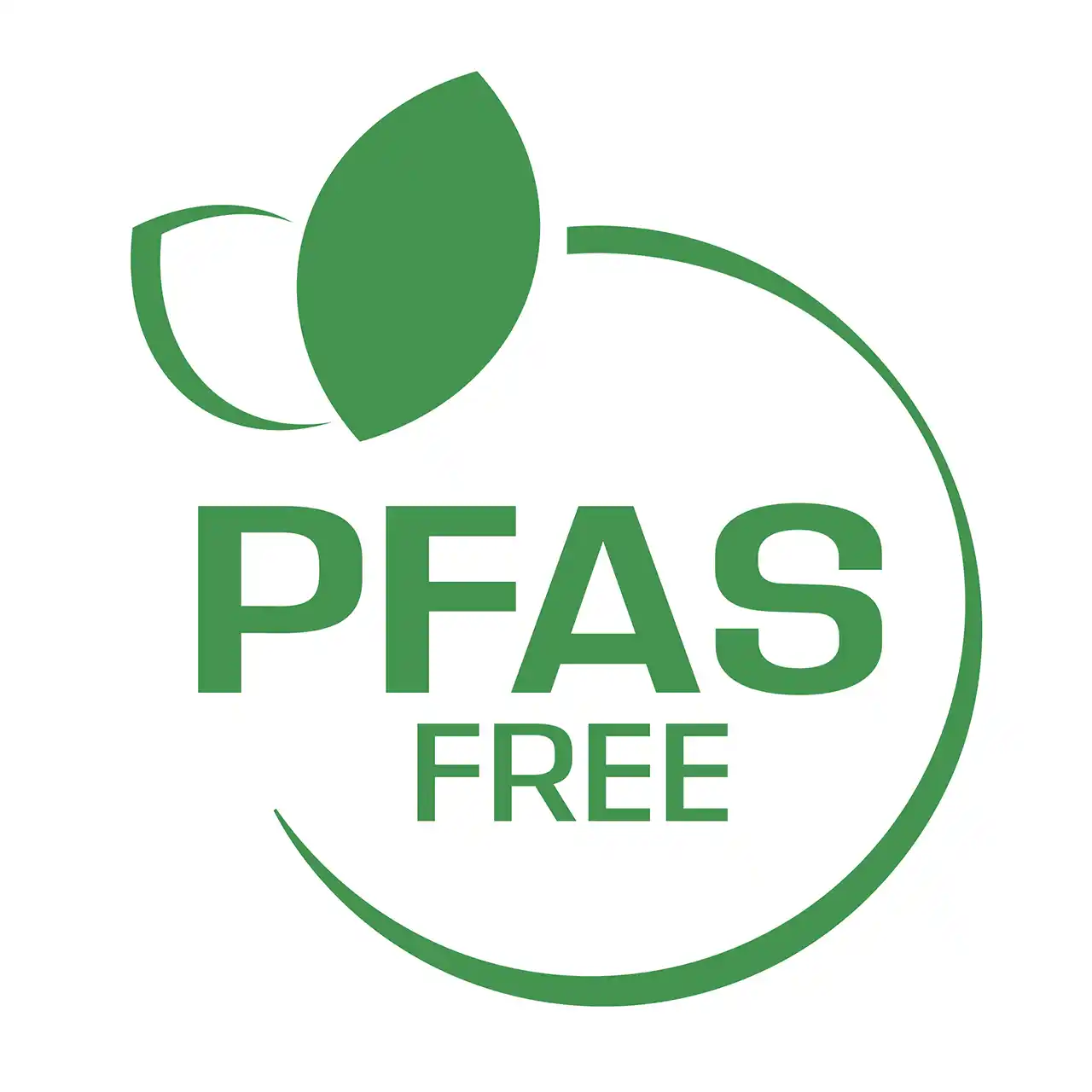
Replacing PFAS entirely is challenging because many of their superior properties stem from fluorine’s unique characteristics, such as its high electronegativity and the strength of the C-F bond. Nevertheless, focusing on specific functionalities, such as heat or chemical resistance, makes it possible to identify alternative materials.
For instance:
- Heat Resistance: Super engineering plastics like PPS (Polyphenylene Sulfide) and aramid exhibit high heat resistance and are strong candidates.
- Chemical Resistance: PPS and polyolefins are suitable options, depending on the chemicals involved. For example, PVA (Polyvinyl Alcohol) may be used in alkaline environments.
- Water Repellency: Although fluoropolymers are unmatched, low-surface-energy materials like polyethylene and polypropylene could be considered under certain conditions.
In addition to material substitution, performance gaps can be addressed through design changes (e.g., altering pore size, density, or thickness) or combining materials to create composites.
Tables 1-4 below compare the properties of commonly used fluoropolymers (e.g., PTFE) with potential alternatives like PPS, PET, and PE. These comparisons help identify materials that meet the specifications required for final products.
Table 1: Properties of Common Fluoropolymers
Polymer Name | Chemical Structure | Melting Point (°C) | Chemical Resistance | Insulation | Non-stick | Weather Resistance | Dynamic Friction Coefficient | |
---|---|---|---|---|---|---|---|---|
PTFE | Polytetrafluoroethylene | -(CF2-CF2)- | 327 | Excellent | Excellent | Excellent | Excellent | 0.04 |
FEP | Fluorinated ethylene propylene | -(C2F4-C3F6)- | 275 | Excellent | Excellent | Good | Excellent | 0.30 |
PFA | Perfluoroalkoxy alkane | -(C2F4-C3F6O)- | 310 | Excellent | Excellent | Excellent | Excellent | 0.20 |
PVDF | Polyvinylidene Fluoride | -(CH2-CF2)- | 171 | Good | Good | Fair | Excellent | 0.39 |
ETFE | Ethylene tetrafluoro ethylene | -(C2H4-C2F4)- | 270 | Good | Good | Fair | Good | 0.40 |
Scroll horizontally to see more.
Reference:
Ogawa, T. (1983). Fusso Jushi no Tokusei to Koatinguzai Toshite no Genjō. 318–327.
Table 2: Heat Resistance Comparison
PTFE | PPS | PET | PE | PA6 | |
---|---|---|---|---|---|
Max Continuous Use Temp (°C) | 260-290 | 200-220 | 80-140 | 100-120 | 80-120 |
Melting Point (°C) | 327 | 280 | 260 | 132 | 171 |
Flammability (UL94) | V0 | V0 | HB | HB | HB |
Thermal Conductivity (W/m.K) | 0.23 – 0.50 | 0.29 – 0.32 | 0.29 | 0.45 – 0.50 | 0.24 |
Reference: Hirose Paper Mfg., created based on articles published on Omnexus (https://omnexus.specialchem.com/)
Table 3: Chemical Resistance Comparison
Chemical | PTFE | PPS | PET | PE (HDPE) | PA 11/12 |
---|---|---|---|---|---|
Acetone @ 100%, 20°C | Resistant | Resistant | Partially Resistant | Partially Resistant | Resistant |
Benzene @ 100%, 20°C | Resistant | Resistant | Partially Resistant | Partially Resistant | Partially Resistant |
Chloroform @ 20°C | Resistant | Resistant | Partially Resistant | Not Resistant | Not Resistant |
Ethanol @ 96%, 20°C | Resistant | Resistant | Resistant | Resistant | Resistant |
Methanol @ 100%, 20°C | Resistant | Resistant | Partially Resistant | Resistant | Resistant |
Phenol @ 20°C | Resistant | Resistant | Not Resistant | Resistant | Not Resistant |
Mineral oil @ 20°C | Resistant | Resistant | Resistant | Resistant | Resistant |
Sodium hydroxide @ 10%, 60°C | Resistant | Resistant | Not Resistant | Resistant | Partially Resistant |
Toluene @ 20°C | Resistant | Resistant | Partially Resistant | Partially Resistant | Resistant |
Xylene @ 20°C | Resistant | Resistant | Partially Resistant | Partially Resistant | Resistant |
Reference: Hirose Paper Mfg., created based on articles published on Omnexus (https://omnexus.specialchem.com/)
Table 4: Surface Free Energy and Contact Angle
Polymer Name | Surface Free Energy | Contact Angle |
---|---|---|
(dynes/cm) | (degrees) | |
PTFE | 19 | 120 |
PDMS (Silicone elastomer) | 23 | 98 |
PVDF | 25 | 80 |
PE | 30 | 88 |
PP | 30 | 88 |
PVA | 37 | 10 |
PPS | 38 | 87 |
PET | 42 | 76 |
Reference:
Ogawa, T. (1983). Fusso Jushi no Tokusei to Koatinguzai Toshite no Genjō. 318–327.
Hada, M. (2010). Purasutikku Firumu no Hyomen Kaishitsu. 78–83.
Reasons for PFAS Regulations
The regulation of PFAS is primarily due to their extreme chemical stability, which, while advantageous as a material property, makes them difficult to degrade in the natural environment. Their persistence and potential for long-term accumulation and dispersal have raised concerns. Although much about their toxicity remains unclear, some PFAS have been evaluated for carcinogenic potential, sparking worries about their impact on the environment and human health. Consequently, PFAS regulations have been implemented and are being increasingly strengthened worldwide. These regulations may include restrictions on PFAS usage in products, setting emission limits, or outright bans on certain PFAS.
The chemical stability of PFAS is attributed to the following characteristics:
1. Strength of C-F Bonds
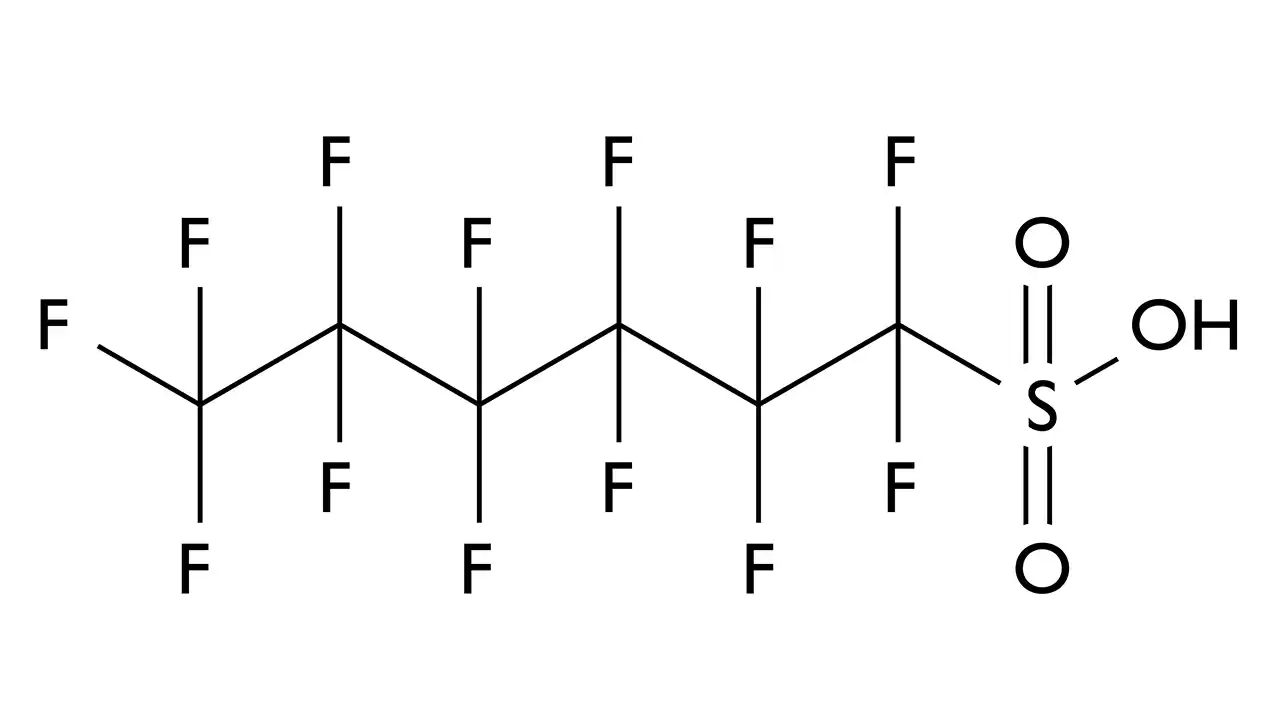
The chemical structure of PFAS contains numerous carbon-fluorine bonds (C-F bonds), which are among the strongest chemical bonds. This provides exceptional resistance to thermal and chemical decomposition.
2. High Electronegativity of Fluorine
Fluorine, being the most electronegative element, strongly attracts electrons when forming covalent bonds. This results in very stable bonds, such as the C-F bond in PFAS, as well as low reactivity with other chemicals, contributing to their chemical resistance and persistence.
3. Hydrophobic and Oleophobic Properties
Due to the high fluorine content, PFAS are both hydrophobic and oleophobic, meaning they resist interaction with water and oils. This property makes them difficult to break down in the environment.
4. Non-Polarity and Low Reactivity of Molecules
PFAS molecules typically feature long fluorinated alkyl chains, resulting in overall non-polarity. Consequently, they exhibit low reactivity and are extremely difficult to degrade through photochemical, thermal, or biological processes.
These characteristics have made PFAS widely used in applications such as water- and oil-repellent coatings, firefighting foams, food packaging, electronics, and cosmetics. However, their persistence and long-term presence in the environment and within organisms have earned them the nickname “forever chemicals,” driving international regulatory efforts to mitigate their risks.
Global Trends
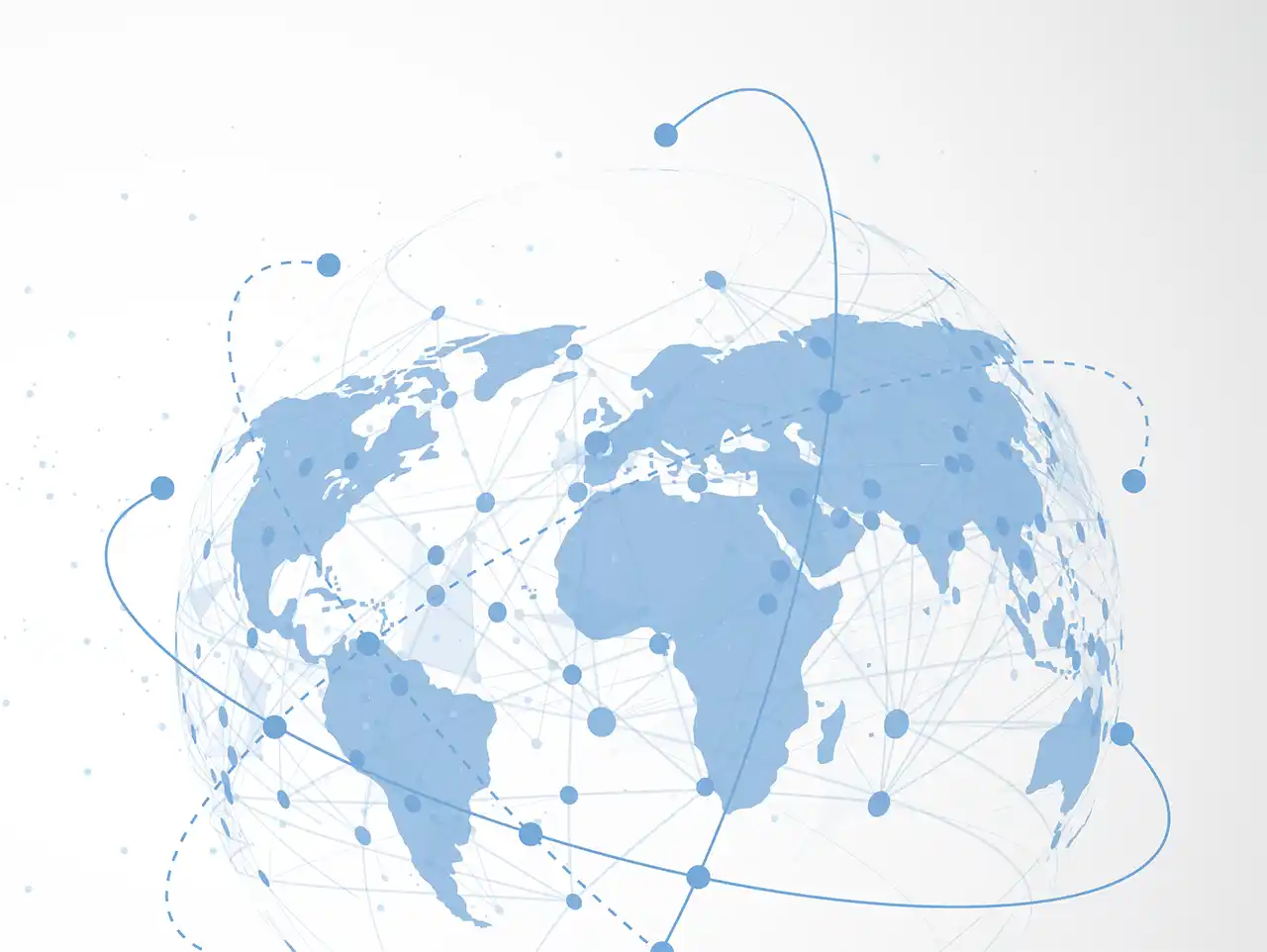
Table 5 summarizes representative PFAS regulations across different regions, highlighting variations in regulated substances and forms, but confirming a global trend toward stricter controls.
Table 5: Examples of PFAS Regulations by Region
Region | Regulation | Regulated Substances | Current and Future Actions |
---|---|---|---|
Europe | REACH Regulation |
|
|
USA | EPA PFAS Strategic Roadmap |
|
|
Japan | Chemical Substances Control Law | PFOS and PFOA |
|
References for Regional PFAS Regulations
- 専門家の気付き~PFAS対策の国際状況と今後の動向~|化学物質国際対応ネットワーク(https://chemical-net.env.go.jp/column_kizuki_matsuoka.html)
- Gleiss Lutz. (2024, March 21). PFAS restriction proposal on the EU level.(https://www.gleisslutz.com/en/news-events/know-how/pfas-restriction-proposal-eu-level)
- EUR-Lex(https://eur-lex.europa.eu)
- New York and California: Bans on PFAS in Textiles and Apparel Begin January 1, 2025 Publications(https://www.morganlewis.com/pubs/2024/11/new-york-and-california-bans-on-pfas-in-textiles-and-apparel-begin-january-1-2025)
- U.S. Environmental Protection Agency. (2024, April). Key EPA Actions to Address PFAS.(https://www.epa.gov/pfas)
- Asahi Shimbun. (2024, July 24). Japan must set PFAS levels to ensure safe drinking water.(https://www.asahi.com/ajw/articles/15359359#)
PPS Nonwoven Fabrics as a Leading PFAS Alternative
In the nonwoven fabric industry, PFAS has been widely used in fiber materials and coatings. Following regulatory changes, there has been increased interest in PFAS-free nonwoven fabrics. PPS nonwoven fabric, in particular, has attracted attention due to its superior properties. PPS, a super engineering plastic, offers high heat resistance, chemical resistance, and mechanical strength, making it a potential replacement for fluoropolymers in certain applications.
Hirose Paper Mfg. has been producing 100% PPS wet-laid nonwoven fabric (“PS”) since 2009, with production records for basis weights ranging from 15 g/m² to 150 g/m² and thicknesses from 30 μm to 220 μm. Table 6 lists representative grades of “PS” products. Custom designs tailored to specific requirements, such as pore size or strength, are also possible. By combining PPS with non-fluorinated coatings, such as silicone, acrylic, urethane, or plant-based options, it is possible to achieve water-repellent properties similar to fluoropolymers.
Learn more about Hirose Paper’s PPS Nonwoven Fabrics here.
Table 6: PS Product Lineup
Product Name | Basis Weight (g/m²) | Thickness (μm) |
---|---|---|
PS0010S | 10 | 30 |
PS0060 | 61 | 150 |
Source: Hirose Paper Mfg. “PS” Datasheet (2024)
Conclusion
While finding a complete substitute for PFAS is challenging, it is possible to identify alternative materials that meet specific application requirements. PPS nonwoven fabrics stand out as a promising PFAS alternative, offering excellent heat resistance, chemical resistance, and mechanical strength.
For inquiries about PFAS-free nonwoven fabrics, please contact us. We will propose the best materials tailored to your needs.